【半導体装置】原因を人から仕組みへ 不良率を半減
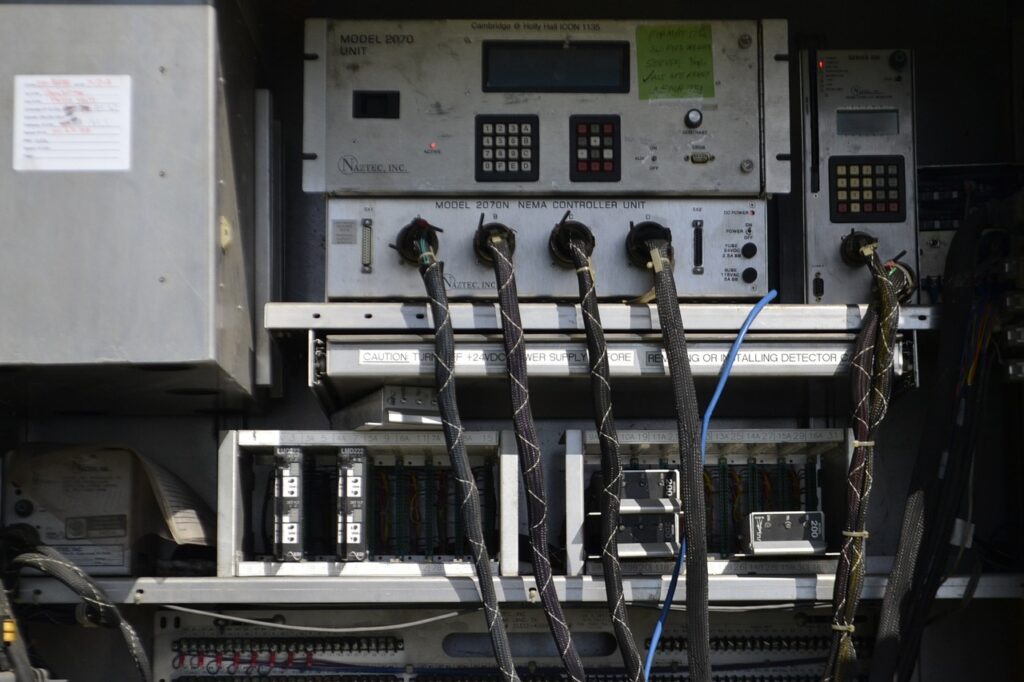
目次
お客様情報
- 関東某県 A社 半導体装置用治具
工程内不良が原因でムダ・ムリ・ムラが
今回の相談は工程内不良の低減。1日あたりの出荷数は10〜20個の装置製造。
こちらを3人の作業者で製造していましたが、工程内不良が9.4%で高止まり。特に特徴である接合技術による原因不明の問題が7割を占めていました。それにより以下のような問題が起きていました。
①1日3時間ほど手直しや解析に追われていた。
②設計と製造で責任の所在があいまいになっていた。
③流出防止のため社内で二重三重の検査が行われていた。
④手直しに備えて、納期1週間以上前から着手するようになっていた。
2023年10月より支援させていただき、以下の手順で解決のサポートをさせていただきました。
伴走型支援でお客様の悩みをオープンに共有
弊社は伴走型の支援をさせていただいております。実験に一緒に取り組んだり、治具を段ボールで試作したり、ときに私も作業させていただいたり。
「私ができないことは、作業の方もできない。」それを合言葉に6ヶ月間取り組ませていただきました。
目標を設定しました
社長様と相談し
2024年3月31日までに不良率50%減
を目標として設定。
同時に、製造リーダーを中心とするプロジェクトチームを結成。月1回の現地訪問と週1回のオンライン会議を行うことを決めました。
改善で取り組んだこととその効果
1. 特性要因図の作成
特性要因図はQC7つ道具にも挙げられている、情報整理する手法です。
プロジェクトが始まった当初は、チームの皆様と特性要因図を作っていくことで可能性を全て洗い出しました。
全員で考えることで、以下のような効果が得られました。
- 4Mの視点で課題が整理される。
- 今まで各自が調査していたことが整理される。
- 手がついていない課題が明らかになる。
初期の頃は何度も特性要因図に立ち返り「どこまで潰し込めたか?」を俯瞰するようにしました。それにより、チームメンバー全員の全員の課題感を揃えることができました。
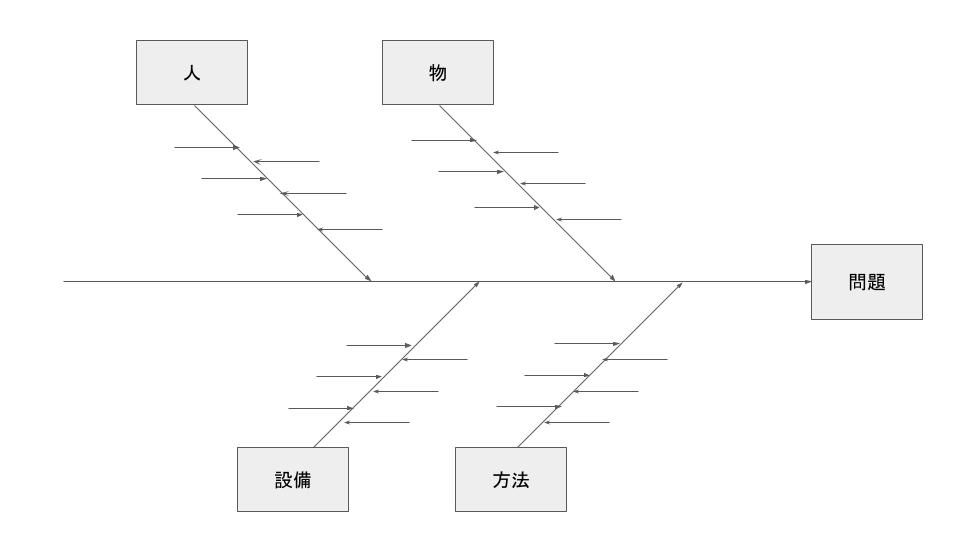
2. QC工程表の作成
工程内不良は接合技術による原因不明が7割を占めていました。構造上、完成状態では非破壊で原因を掴むことができません。ですので、改めて各工程で何を保証しているか整理しました。工程での関所を機能させ不良を取り除き自然減を狙うことにしたのです。
QC工程表を作ることで、以下のような効果を得られました。
- 作業者による作業のばらつきが認識された。なぜその手順をやっているのか?ベテランから引き継ぎきれていないことが明確に整理し標準化できた。
- 接合作業の1工程が手作業により工程能力が確保できていないことがわかった(Cp,Cpk<1.33)。設備化の再チャレンジを行い接合条件の安定化ができた。
3. やりにくい作業の撲滅
作業観察をしていくと、同じ品番でも製造時間にばらつきがあることがわかりました。平均より4~5時間も長くかかることがあったのです。調べてみると治工具が不足しているため時間ばらつきが発生していることがわかりました。
- 組付け治具:調整しながら組んでいたものを、置くだけで位置が決まるように。
- ポカヨケ治具:組付け方向を確認しながら組んでいたものを解消。
段ボールで試作品を作ったり、原理品をその場で作ったり。直接的に作業が楽になるので、作業員の方々から積極的にアイデアが出てくるようになりました。また、複雑な作業工程がメンバーの生産性を下げ、不良の一因となっていることが再認識されました。現在は、本来の治工具手配はどうあるべきだったのか?を議論し、より強い製造体制づくりに取り組んでいます。
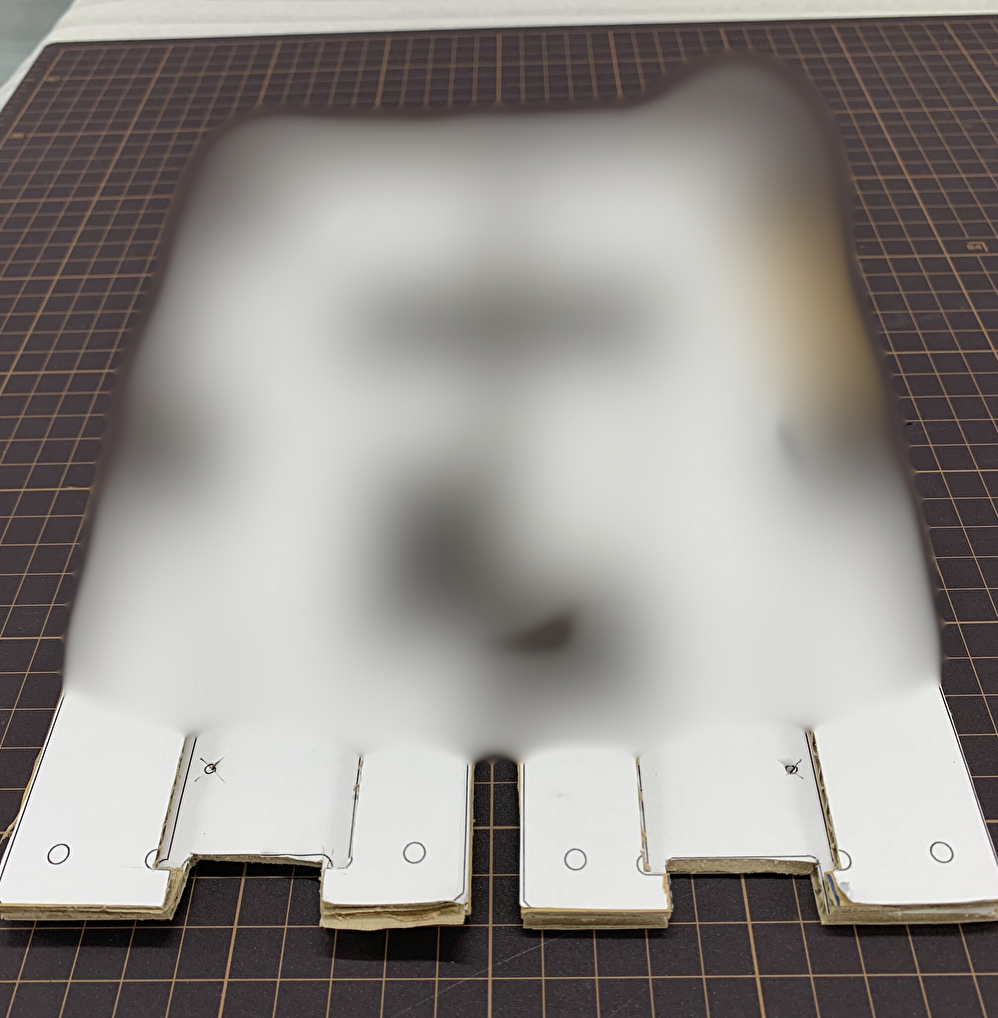
段ボールを使った試作品
4. 推進体制を変更
原因不明の不具合が7割だったことから、再現実験を行う必要がありました。また図面の情報が足りていないこともわかってきました。いいものを作るための条件指示が足りなかったのです。つまり、当初は製造の問題と認識していたものが、設計の方にも手を動かしてもらう必要がでてきたのです。
製造だけでなく設計も巻き込んだ改善となるため、社長様にお願いし体制を変更することに。設計、製造を統括するポジションの方まで推進者を上げてもらいました。
これにより以下のような効果を得られました。
- 課題の推進者が明確になった。
- 日常業務とプロジェクトの優先度が明確になった。
QCサークルなど、プロジェクト的に進める仕事は日常業務とのバランスが難しくなります。しかし、優先順位が判断できる職位の方が参加することでメンバーは安心して仕事することができました。
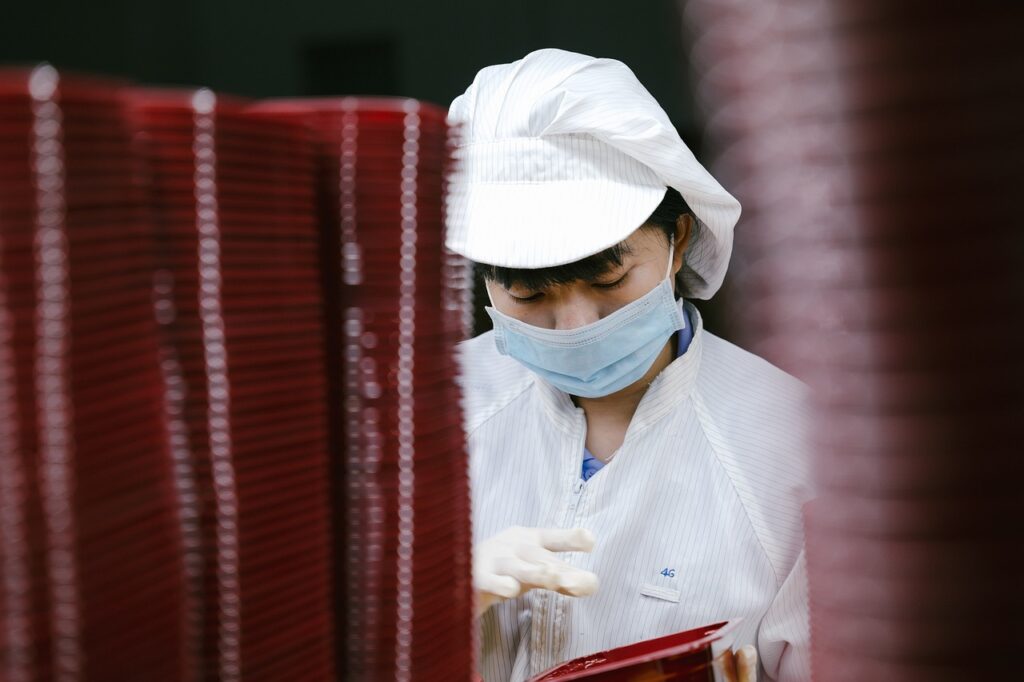
想定以上の成果を達成!
取り組みから6ヶ月。不良率は9.4%から3.4%まで減少。何よりも原因不明の不具合が0%になったのです。長年原因不明で責任の所在があいまいだった問題が、技術課題として可視化することができました。
私も初の接合技術でしたが、メンバーの方々の知識に感化されあっという間の6ヶ月でした。
品質の改善だけでなく、さらなる企業価値向上のため現在は以下の課題に取り組んでいます。
- 課題解決の仕組み化:会社全体で異常に気づき不良を是正していく動き。
- 二重検査の廃止:不良が発生しない体制を作り、検査を辞めていく。
- リードタイムの短縮:出来るだけ早くお客様の要望に答える体制。
引き続きA社様には関わらせて頂く予定です。圧倒的品質と圧倒的短納期に向けてサポートさせていただきたいと思っております。
お客様の声
中小企業では、必要な専門スキルを持つスペシャリストが不足しており、問題の本質に迫ることができず、表面的な解決にとどまることが多いです。
問題を体系的に理解し解決するために、外部の専門知識を活用することが重要だと、今回の改善を通して実感しました。慢性化していた問題を6ヶ月で50%減させることができ、何より原因不明の不具合をゼロにすることができました。外部に伴走してもらい生まれる成果は、従業員の自信と意欲を高め、好循環を生み出すきっかけとなっています。なので数字に見えている範囲は小さくても、 もっと広がりが出るだろうという期待が、今はあります。
中小企業が全ての業務を内製で処理するのは本当に難しいです。
確かに経営者や従業員が新たなスキルを学ぶことも重要ですが、外部の力を借りる方が効率的です。しかし、外部利用には資金が必要です。ですが1度でも活用することで成功体験を得ると、そのメリットと価値は明らかになると思います。
田代さんには、引き続きサポートいただく予定です。今後もよろしくお願いします。