品質管理はいらない。「目利き」が現場を救う。
「品質管理なんて、いらないんじゃないか?」
そう思ったのは、何社もの町工場を支援してきたある日、ふとした違和感からでした。
私はもともと品質管理の出身です。トヨタで技術者として働き、データを分析し、不良の再発防止に奔走していました。
「なぜ不良が出たのか?」「どう管理するか?」
そんな問いに真剣に向き合ってきた身として、このタイトルはまるで“自分への裏切り”にも聞こえます。
それでも、あえて今回はこの仮説を提示してみます。
「元・品管」が語る、品質管理いらない説
前述の通り、私はトヨタで16年間、品質管理の仕事をしてきました。
図面や工程を検証し、「何の特性を担保するか?」を決める。
そして、それを日常管理に落とし込み、良いものがずっと作られる体制を作る。
「なんとなく良い」を数値化し、それを仕組みに落とし込む。
ものづくりから感情を排除していくことが仕事でした。
でも今、「品質管理がいらない」と思っています。
そして、その代わりになるのが、「目利き」。
数値や帳票ではなく、人の目・感覚・経験――まさに「この人が見てるから大丈夫」という世界。
これは、品質を軽視しているわけではありません。むしろ逆です。
形式的な管理より、現場の目利き力の方が品質を守っている。
そんな事例を、私は何度も目の当たりにしてきました。
これはどんな町工場の話か?
あらかじめ断っておくと、今回の仮説は「中小製造業」を想定しています。
社員でいうと100人以下。
会社機能としては、総務、営業、購買、製造といった感じでしょうか?
お客様との信頼関係と、現場の職人の技術で、日々の仕事が着実に回っている――そんな町工場です。
そんな工場にこそ【目利き】の力が必要です。
とある金属パイプメーカーでの話。
ある会社の事例で説明しましょう。
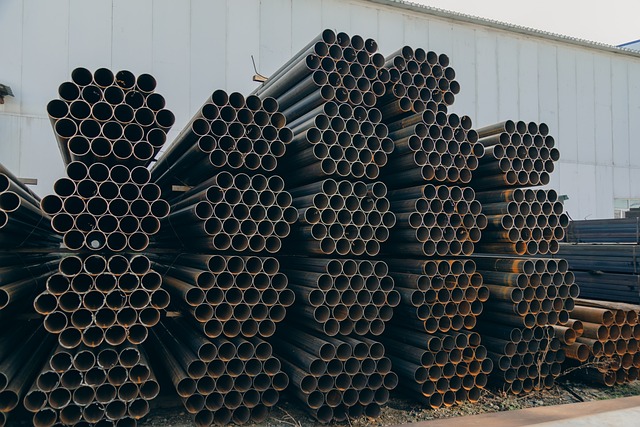
イメージ図
とある金属パイプメーカーでは、5台の設備を使って切断していました。
パイプの径が変わると設備セットアップに時間がかかるため、径によって使う設備がわけられていました。
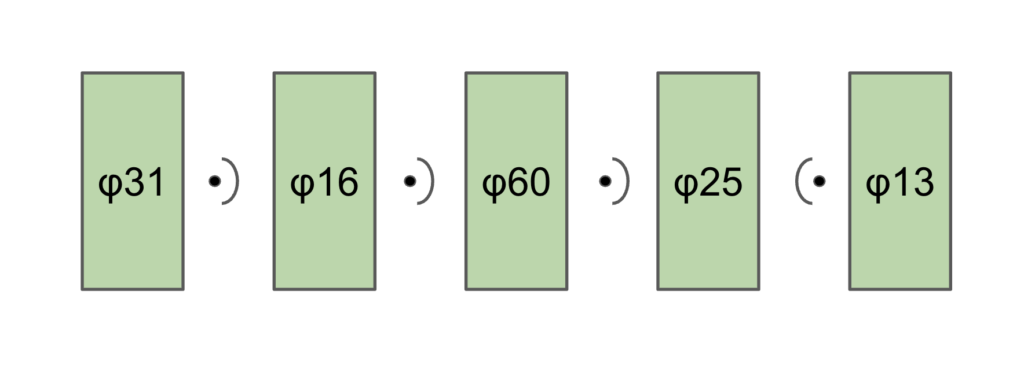
設備レイアウト
しかし、品質問題がたびたび発生。
キズやサビがお客様へ流出し、営業さんが謝ることが発生していました。
まさに「品質管理」が必要な場面です。
ここで弊社が参画。
前職の私でしたら
- 検査項目を決める
- 必要な照度を確保する
- 限度見本を作成する
など、いわゆる「品質管理」の仕事をしていたでしょう。
しかし、【目利き】の力を信じます。
人はもっとできるはず!その仕組を構築します。
まずは、出荷履歴を取り寄せ、顧客別にABC分析することにしました。
すると上位2社が20%を占めていることがわかりました。
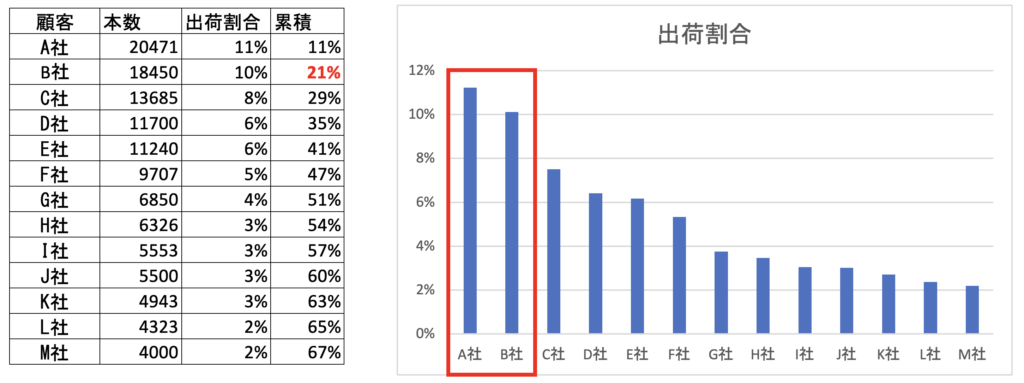
出荷履歴の顧客別ABC分析
これにより、設備5台のうち1台(20%)が、A社B社専用にできることがわかります。
そして、作業者も合わせて専用になってもらいました。
この作業者の方には、A社B社の方とも会ってもらい、関係を構築。
お互いに名前で呼び合う関係になりました。
顔の見える関係、ですね。
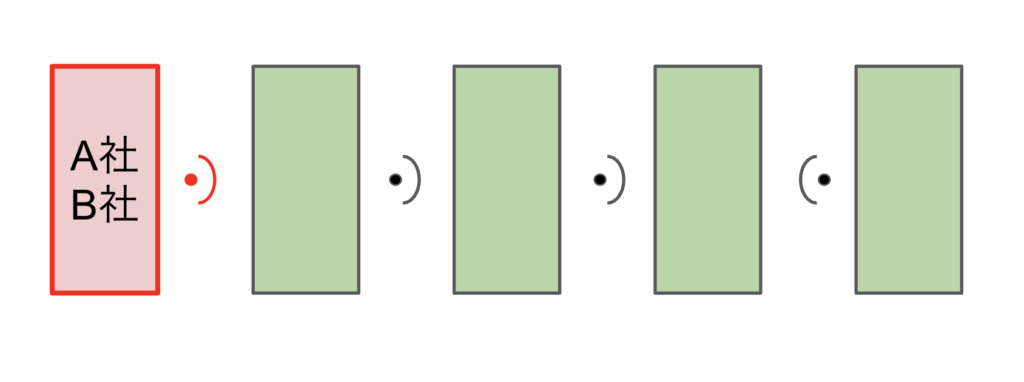
新しい設備割り振り
もちろんこの方法を採用すると、径の変更が度々起こるので、セットアップが何度も発生します。
しかし、作業者の【目利き】の力が発揮されます。
- お客さんは、どのパイプを何に使っているのか?
- どんな品質で出せば良いか
- いつどんな注文が来るか
まるで顧客先の社員のように【目利き】を発揮し、良品を作るようになるのです。
もはやそこに、たくさんの品質帳票は不要です。
懸念だったセットアップも何回も繰り返すうち、そのスピードが向上します。
これで、従業員が自らお客さんのためを思い、パイプを切断する工場ができあがります。
これにより、クレームは一切なくなりました。
今、こちらの工場では、お客さんの要望に答えるため「曲げ」工程の取り込みを検討しています。
これも従業員からの発案。
売上もアップし、もはやとどまることを知りません。
目利きが全てを変える
製造業は、お客様を見失いがちです。
もちろん、私の前職のような大企業であれば、お客さんとの距離は必然的に遠くなります。
だから、品質管理のような仕組みが必要でしょう。
でも、中小製造業はお客様が見えます。
従業員の【目利き】を信じ、一人ひとりを誇り高き職人にしたて、より付加価値の高い仕事をする。
それが、ものづくり日本の進む道だと思います。
工場改善サービス株式会社といっしょに
弊社は「社長より先に作業着を汚すコンサルタント」として、一緒に人を活かす工程づくりをしていきます。
もし、ご興味を持って頂けたら、お気軽にお問い合わせください。
まずは、工程の基本5Sから始めませんか?
今なら【5Sチェックシート】をお配りしています。資料請求よりお問い合わせください。