日本のカイゼンはタイで通用するか?1日でムダ発見するコツ
先日、3泊4日でタイにあるカーペット工場を訪問し、5S改善の支援をしてきました。
- 言語も文化も違う、初めて訪れる工場。
- 改善活動の習慣も根付いていない現場。
そんな環境でも、たった1日で90万バーツ(約400万円)相当の効果を生み出すことができました。
目次
なぜ初訪問の工場で、これだけの成果が出たのか?
その背景には、現場の力を引き出す“2つの鍵”がありました。
このブログは、こんな方にオススメです:
- 何か工場を変えたほうがいいけど、具体的な方法がわからない
- 変更することに対して、従業員が反発する
- 他社を見る機会があるけど、視点がわからない
- 工場経営が儲かっていない、もしくは儲かっているかどうかもわからない
ぜひ、最後まで読んでいってください。
改善対象の工場
今回改善したのは、カーペットの圧着~トリミングの工程でした。
これまでは、3台の機械に対し4人で対応。
「まとめて生産」していたため、忙しさの波が激しく、ムダな待ち時間や人の遊びが発生していました。

ここに“ペースメーカー”の概念を取り入れ、常に一定の流れで作業が進む仕組みを導入。
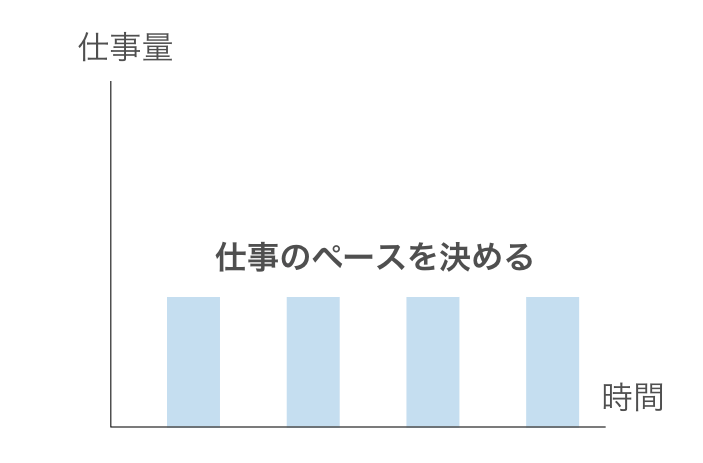
結果、必要な人員が2人に削減され、稼働の平準化にも成功しました。
イメージで言うと——
池の鯉がドバーッとエサに群がるような動きから、
観賞魚に少しずつエサをあげるような、落ち着いた流れへ。
そんな改善でした。
成果が出た2つの理由
①「ムダ取り」という視点をぶらさなかった
改善の基本は“ムダをなくすこと”。
どんな国、どんな業種であっても、
“ムダ”を見つけて減らす視点があれば改善は可能です。
「ウチの工場は特殊だから改善できない」とよく聞きますが、
実はどの現場も“原理原則”は共通です。
※詳しくはこちらのブログでも紹介しています👇
↓↓↓
https://koujou-kaizen.co.jp/【教科書レベル】5sが続かない理由、9割は「やる/
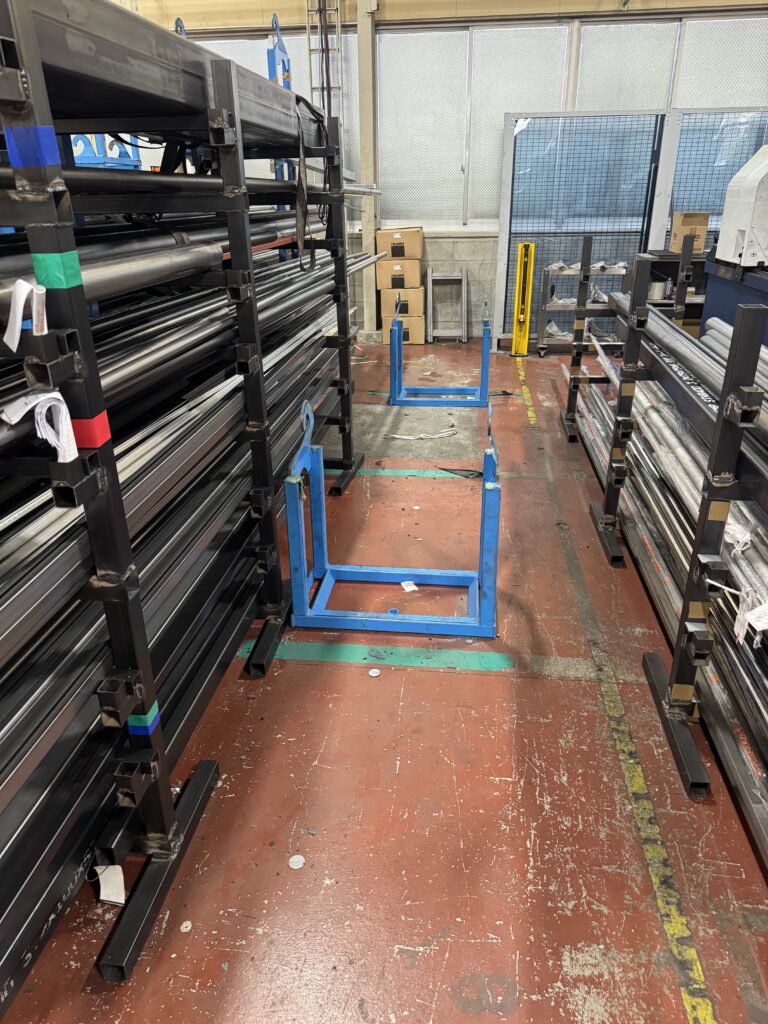
②手を動かしたから、言葉を超えた
言語が通じにくい海外工場でも、実際に改善をやってみることで共感が生まれました。
ブランコは、揺らさないと動きません。
同じように、現場も手を動かすことで変わっていきます。
「うちの現場は動かない」と言っている経営者の皆様、
まずは自らが手を動かしてみることをおすすめします。
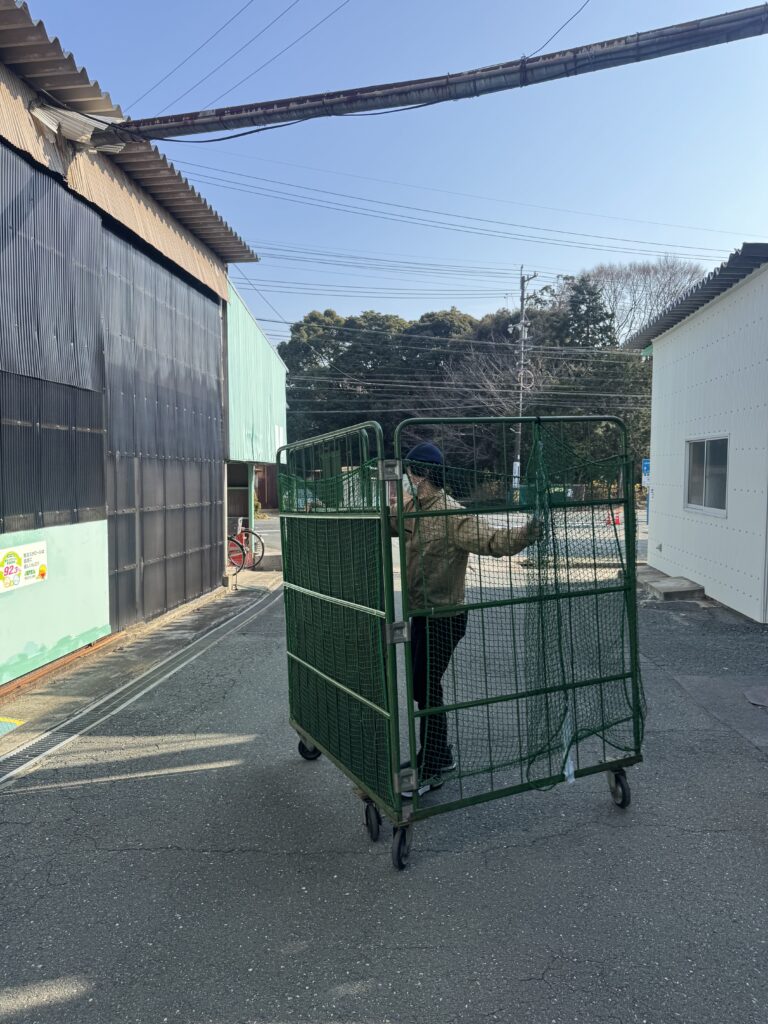
実は「日本の改善」だった
実は、今回の改善を通じて私自身が一番ハッとしたのは、
「これは日本でもやるべき改善だったな」ということ。
タイの工場も、今は安価な人件費に支えられていますが、
物価は確実に上がってきており、将来は見直しが迫られるかもしれません。
でもこの構造、日本の地方工場でも同じことが起きていますよね?
今は利益が出ているから、課題を先送りにしていないか?
本当は気づいているのに、動けていない課題がないか?
そんなことを自問しながら、今回の改善を通して、
「これは海外の話ではなく、日本の経営にも刺さる話だ」と強く感じました。
世界で通用するカイゼン手法
今回は、タイの現場で通用した**“どこでも使える改善の原理原則”**についてご紹介しました。
もっと具体的な改善ノウハウを知りたい方には、
工程チェックシートお届けしています。
- 他社の改善事例を知りたい
- 自社に合った改善の進め方を知りたい
- 現場で使える改善の“言葉”や“仕組み”を知りたい
そんな方はぜひ資料請求ください✨