【発泡スチロール】赤字から黒字へ。現場改善のすべてを公開
目次
発泡スチロール成形企業の改善(1期振り返り)
お客様はどんな状態だったのか
東海地域に位置する従業員30名の発泡スチロール製造A社は、原価高騰により直近2期は厳しい経営状態にありました。また、創業から70年を迎え、次期経営層の育成も緊急課題として浮上していました。
① 厳しい経営状態の打破
② 次期経営層の育成
この2つの課題を乗り越えるべく、弊社と改善プロジェクトを開始。2024年6月をもって1期分の支援が完了しました。
今回は
- どんなプロジェクトを
- どのように進行し
- どのような結果になったか
についてご紹介いたします。
プロジェクトの目的と現場改善メニュー
今回のプロジェクトの目的は2つ。
- 企業の持続可能な成長を実現すること
- 現場から経営を変える改善を行うこと
です。
このプロジェクトでは、問題の特定から解決に至るまでの一連でフェーズに応じた取り組みを実施。現場改善のためのフルメニューでサポートいたしました。
半世紀変わっていない製造の考え方を大きく変えること、そして次世代の人材育成に必要なのは、そこで働く方々の知識やマインドの変化です。
そのため、社内セミナーを重点的に行い、リーダーの心構えやプロジェクトマネジメント手法を伝授にも努めました。
【フェーズ①:現場の課題を確認】
まず、大切なのは「最初に取り組むべき問題」の把握です。言い換えると「センターピンの特定」で、これを行うと解決すべき事項の優先順位がわかります。
把握するために
- 物と情報の流れ図(下記図)を作成
- 工程能力の把握
- 経営者と従業員へのインタビュー
を行いました。
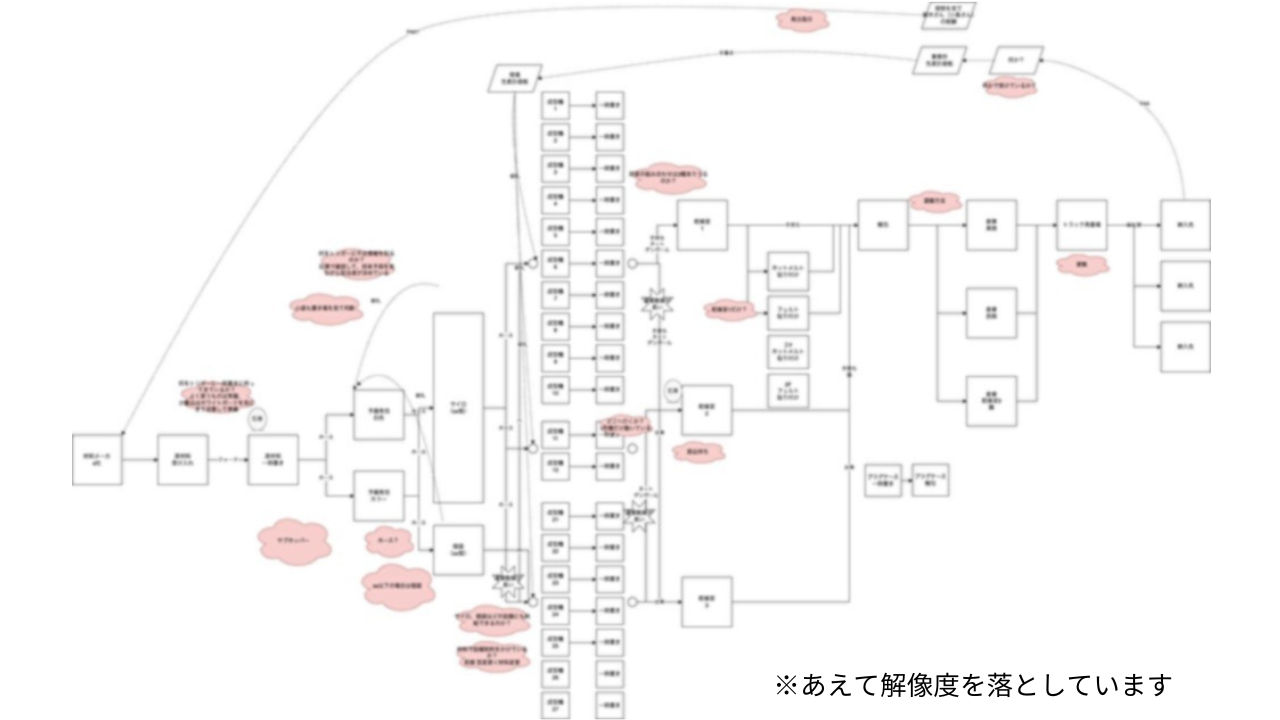
その次に、取り組むべき問題を解決する「プロジェクトチームを結成」します。ただ、いきなりチームを結成しても現場のスタッフは混乱するので、
- プロジェクトマネジメント手法
- リーダーシップの極意
について、しっかりと伝授し自走できるように人と環境を整えました。
【フェーズ②:診断結果を元に実行】
問題の把握とチームを結成したら、次は実行のフェーズです。月に1~2回の頻度で訪問し、オンラインも活用しながら下記のようなサポートを行いました。
- ムダ取り活動
- トヨタ生産方式(TPS)セミナーの実施
- 5S(整理、整頓、清掃、清潔、躾)活動
- 工程内不良低減活動
- 進捗ミーティング
すべて改善プロジェクトの一環ですが、そのうち利益率に直結する「ムダ取り活動」をどのように進行したのか、具体的にお伝えします。
もし良かったら参考にしてみてください。
ムダ取り活動の具体的な実施方法
問題の整理と発生の背景
この企業が抱えていた問題には、以下のようなものがあります。
- 期末在庫の増加
- キャッシュフローの悪化
- 保管スペースの増加による生産スペースの圧迫
- 探すムダ、運ぶムダの発生
- 工程内不良の悪化
- 必要人員がわからない
では、なぜこんなことが起きたのでしょうか。問題発生の背景を探ってみると、
◎高度経済成長の名残から設備稼働率(設備は止めるな、という思想)が中心で、上流からの押し込み生産になっていたこと
◎上流工程と下流工程が連動していないため、工程は仕掛品であふれていたこと
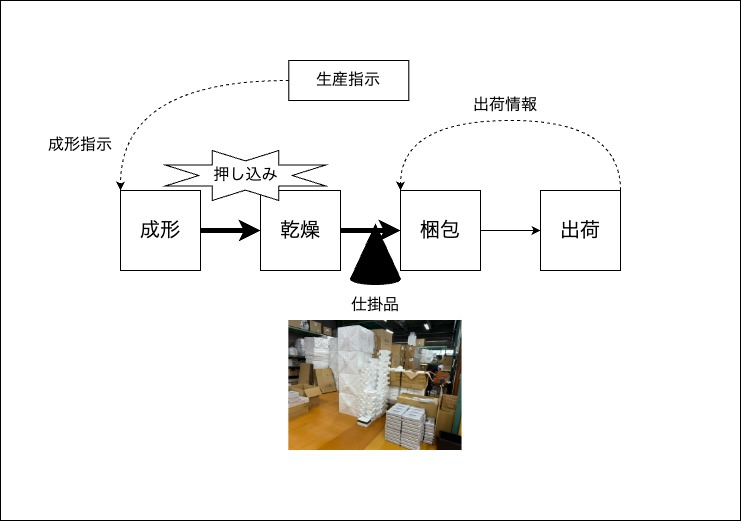
が分かったのです。生産ラインにおいて在庫やムダをなくすことが必要なのに、工程の異常や過不足が分からない状態に陥っていました。
問題を解決するための対策
「設備は止めるな」という設備稼働中心の考え方から、「売れに合わせた生産」をし、いかに「売れる数だけを安く作るか」という考え方に変えていきます。一気に変えられる部分ではないので、これも1ステップずつ進んでいきます。
【ステップ①:出荷の見える化と原単位の決定】
出荷の見える化を進めて仕掛品の低減を実現しました。出荷管理表を作成し、工場全体が出荷に合わせられる体制を構築。
また、工程感の運搬単位を「持てるだけ持つ」の手運搬から「1台車分」に基準化。これにより、台車のまま次の工程へ投入でき、【 100時間/月 】の工数低減を達成しました。
しかし、現場からは「台車が足らなくなるかも」といった変更に対する不安が寄せられました。そのため、まずは品番を限ってトライアルで実感してもらい、徐々に他の品番にも水平展開しています。
【ステップ②:ロットサイズを半減】
成形と梱包間の仕掛品滞留が常態化していた問題においては、出荷ロットサイズに対し、ロットサイズの大きい順の上位3割を半減させることで【 250万円相当 】の仕掛品在庫を低減。結果、【 床面積50㎡を創出 】しました。
【ステップ③:人材育成】
全従業員の底上げを目指し、改善風土を醸成するためのムダ取りセミナーを2回開催。
従業員の知識の底上げを図ることで現場の見える化も進みました。5S活動の1つでもある「赤札大作戦」を実施して【 30品目以上の不要物を撤去 】し、工程の遅れや進みが分かる職場づくりを支援しました。
また、常にプロジェクトリーダーの工場長の壁打ち役として、人材育成・採用・多能工化についてのアドバイスを提供しています。相談先がいない状態での工場運営ですが、私と会話することで考えがまとまり、積極的な発言が生まれるようになりました。
改善プロジェクトを1年行った結果、今期は黒字に
半世紀以上変わらなかった製造の土台となる考え方を大きく変えるのは、文字通り「大変」なこと。スムーズに進まないこともありましたが、セミナーや現場でのトライアルを通じて、今では現場の理解も進み少しずつ成果が出てきました。
これらの取り組みの結果、同社は生産効率の向上とコスト削減に成功!今期は赤字を解消し、黒字で着地しました。期末在庫も10%低減、床面積で50㎡の活スペースが生まれました。
また、次期経営層の育成プログラムも進展し、リーダーシップの強化が図られました。改善風土の醸成によって従業員モチベーションと協力体制が向上し、持続可能な成長の基盤が確立されました。
今回サポートさせていただいた同社の社長からは、以下のような嬉しい声をいただきました。
赤字打破に悩んでいたが、現場に入って改善活動をしてもらったことで円滑な生産ラインが確保できた。また、人材育成のサポートも手厚いので、これからも工場長に寄り添ってメンバーのやる気を引き出すポジションとして、次期経営者とともに歩んでほしい
◎厳しい経営状態の打破
◎次期経営層の育成
この2つの課題に対して結果を出せたことも嬉しいですし、向き合ってくださった工場長と従業員の皆さんにも感謝の気持ちでいっぱいです。引き続き、更なるリードタイムの短縮とメンバー育成に尽力していきます!